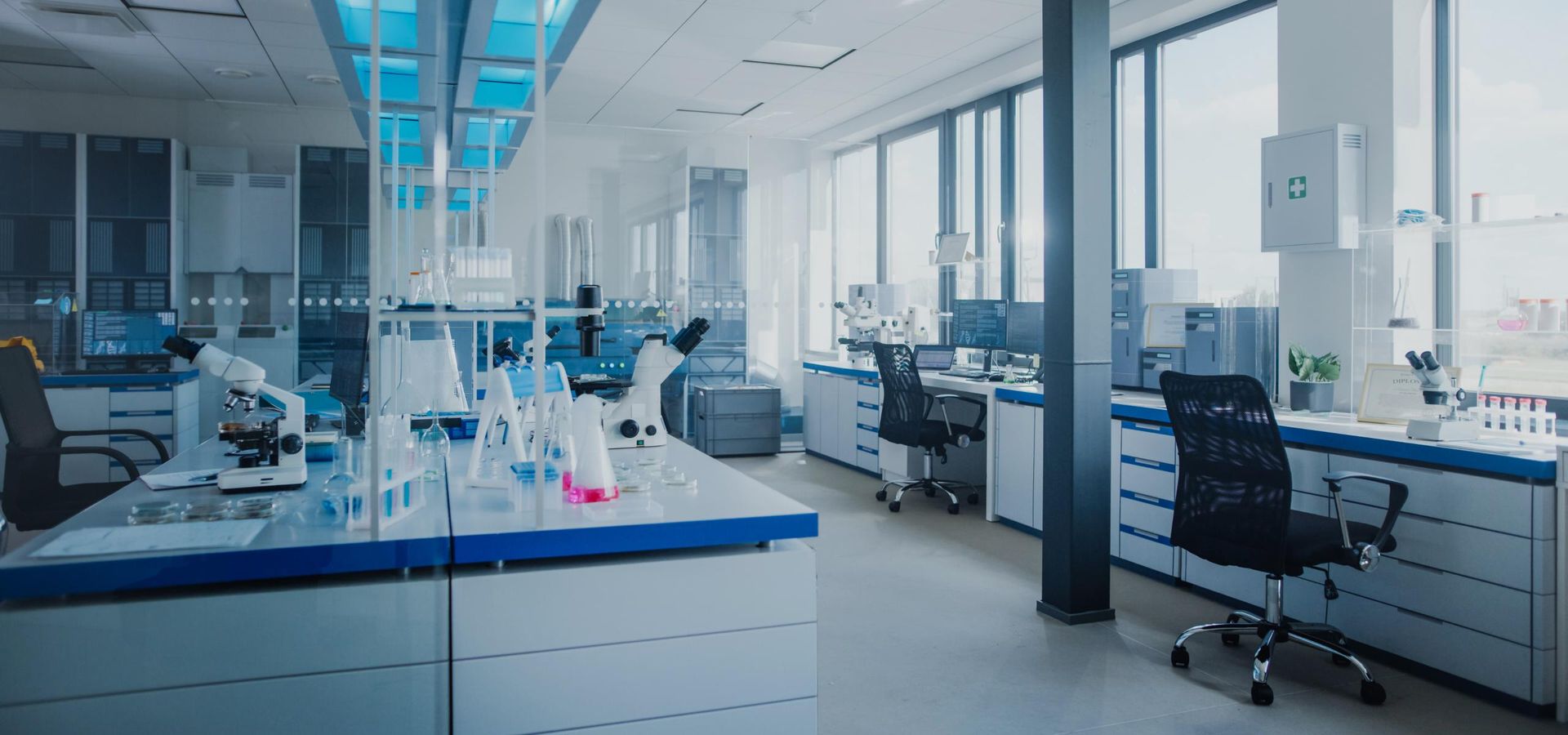
Medical equipment management software
During 10+ years of cooperation, Itransition has developed seven versions of the medical equipment system that helps collect and manage blood data for close to 400 blood centers and labs.
Context
Terumo Blood and Cell Technologies is a medical technology manufacturing company with 7,000 employees around the world. Founded in 1965, the company has become a global leader in transfusion medicine, therapeutic apheresis, and cellular technologies, delivering products and services for clients and patients across 130+ countries.
The customer needed a solution that can receive and process data from Terumo devices as well as manage and monitor them. This is why they hired medical device software developers from Itransition to create TOMEs (Terumo Operational Medical Equipment Software) — an operational management solution that automatically integrates and manages multiple medical devices and their data in real-time.
Solution
During our partnership with Terumo, Itransition has developed seven versions of TOMEs software. In addition to the main system, we also created TOMEs Stations – a module that connects peripheral devices to the stations.
TOMEs
Itransition began by analyzing the customer’s blood center devices, which include automated blood collection and blood processing systems, automated component extractors, sterile tubing welders, handheld barcode readers, and third-party scales. TOMEs interact with standalone Terumo devices, enable collecting and managing their session data, and communicate with other customer systems.
TOMEs also support 22 languages, including English, Russian, German, Chinese, and Dutch. The solution ensures blood safety while being cost-effective and can be implemented and integrated during all supply chain stages (blood collection, processing, storage, etc.). Linking other devices with a blood center and data management systems enables blood center companies to build a network that helps support procedural decisions, drive compliance and traceability, speed up donations, ensure process control, and improve their efficiency and productivity.
TOMEs features:
- Bi-directional communication with information management systems
- Customized process control
- Electronic data capture
- Intelligent barcode configuration
- Centralized device settings
- Device and procedure status monitoring
- Custom reporting and procedure data export
- Operator management and authentication
- Procedure priority list management
- Interoperability among TOMEs-connected devices
Â
This feature set brings TOMEs’ users multiple benefits. For example, electronic data capture ensures fast and easy record-keeping, records accuracy and security, improved traceability and compliance, and minimized manual data entry and errors. Intelligent barcode configuration, in the meantime, allows the creation of barcodes for identification and sharing of the information about supplies, incidents, operator ID, donation ID, sample tubes, etc., capturing manual steps and observations, and validating procedure data against blood bank information system data to enhance blood donor safety. Bidirectional communication also offers such advantages as seamless data transmission, instant data delivery, data protection from loss and unauthorized access, and GDPR compliance.
To manage and monitor devices and configure different device settings and parameters, operators need only a PC.
The data record of each session contains different values, such as blood product type, volume and weight, time and date of blood sampling, etc. Users can create customized data views filtering by location, station, program version, users, events, specific parameters within a process, etc.
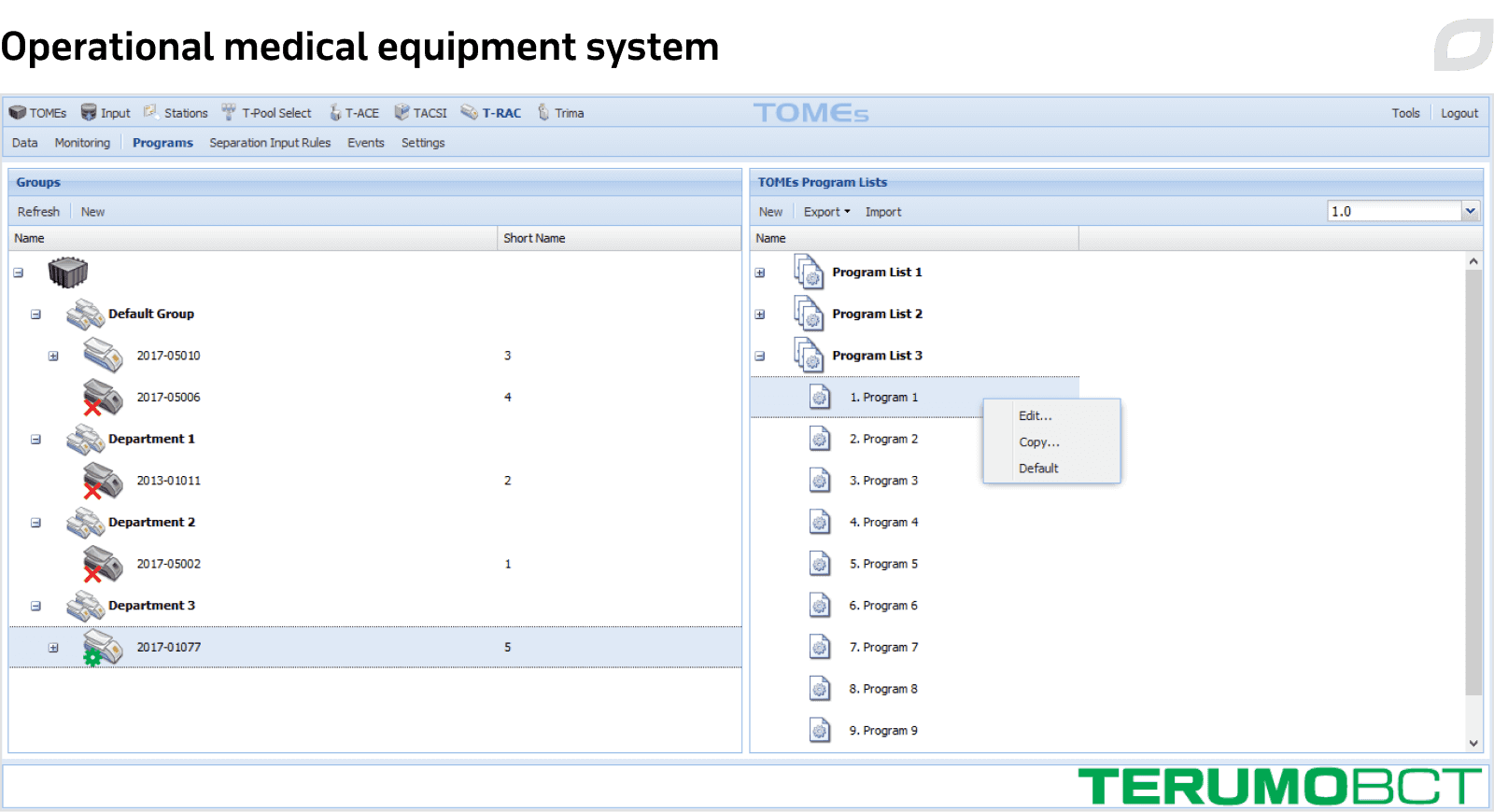
The developed solution automates the following processes:
- Blood data collection and management
- Data integration into the blood center information system
- Data verification and process control
- Data export in different formats, including XML, TXT, EXC
- Device management and monitoring
Peripheral devices module
Under TOMEs, the module concept is based on combining several peripheral devices of different types and manufacturers into one station, allowing leadership to manage them through a single interface. The module and its programs are created and configured in TOMEs, with the session data from the module automatically exported to TOMEs.
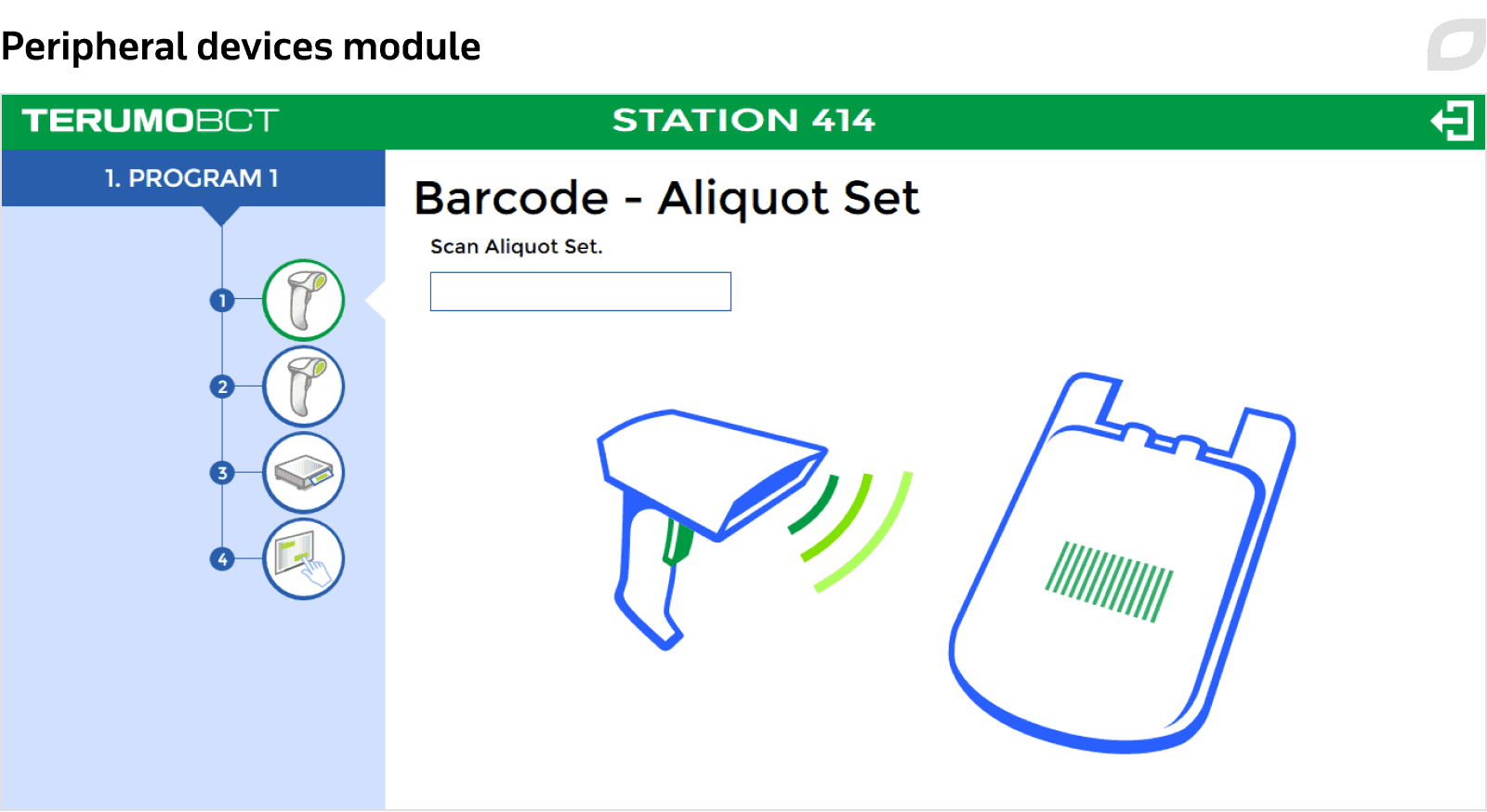
Compliance
Together with Terumo, Itransition developed the medical equipment solution and prepared its documentation in accordance with the requirements of IEC 62304, an international standard for medical device software.
The full TOMEs suite, including device connectivity, is available in countries that accept the CE Mark under the European Union Medical Device Regulation. TOMEs Stations have FDA clearance and are available in the US. As a medical device manufacturer, Terumo ensured the solution complies with the FDA’s Good Manufacturing Practice and Medical Device Reporting requirements. The company’s quality control system and infrastructure for producing life-sustaining devices is fully compliant with European Union and FDA regulations.
The solution is also compliant with HIPAA, an important patient data protection standard. The customer ensured the protected health information used in the solution has physical, network and security measures in place.
Multiple device connection
Customer devices can send data every 10-15 minutes. With hundreds of devices accumulating data over time and some clients having device-heavy infrastructures, the customer was challenged with integrating a large number of medical devices. To solve this, we optimized the software, improved its performance, and allowed clients to connect hundreds of devices simultaneously.
Process
Itransition was responsible for the whole project, including business analysis, development, integration, testing, maintenance, and support stages. During the requirements elaboration, our team communicated closely with Terumo to fully describe necessary features, identify and prevent possible issues, advise the most appropriate options and alternatives for technical implementation, as well as suggest technical improvements.
Early in the project, we couldn’t work with real devices, so our team used emulators for software development and testing. At the moment, however, Itransition has access to all real devices in-house and continues to develop and test the medical software.
During the software testing stage, we performed the following tests:
- Smoke auto tests
- New feature testing and defect validation
- Full regression testing
- Cross-platform and cross-browser testing
- Localization testing
- Integration testing
Collaboration
Terumo’s team is distributed across the US, EU, and Asia. The main part of the system is developed by Itransition but additional components were developed by the customer’s US team and other tech vendors. The US team created the medical devices themselves, while Itransition’s team, consisting of a project manager, a Scrum Master, a business analyst, 14 developers, and 4 QA engineers, was responsible for developing integration software.
During the collaboration with Terumo, we first adhered to the Open UP framework and then shifted to Scrum, working in a regular two-week sprint. Itransition’s project manager and Scrum Master communicated with the customer’s Product Owner daily, held several calls per week with the customer’s office, and every quarter arranged face-to-face meetings either at Itransition’s office or at the customer’s headquarters.
Requirements management
In the healthcare domain, special attention is paid to requirements since late changes, hot fixes, and new product versions are difficult to release. During our long-term collaboration, we went through many requirements specifications using the following set of tools:
- Confluence to store software requirements specifications
- Jira for task tracking
- TestRail for test case management
To prevent the duplication of requirements for the further versions of medical equipment software, we created a document named Global SRS stored in the same internal requirements management system but in a separate section. The Global SRS approach ensured that:
- Initial requirements were received the same way (Word document + supportive documents)
- The requirements were added to the internal requirements management system
- Once the requirements were analyzed and clarified, they were added to the Global SRS
When the Global SRS accumulated hundreds of pages, we shifted to a more effective solution and created a single requirements document for both Terumo and Itransition teams.
Results
Over the course of a 10+ year partnership, Itransition has developed seven versions of TOMEs, a software solution designed to help blood centers and lab operations collect and manage a large amount of data related to the collection, processing, and storage of blood. Nowadays, around 400 blood centers around the world employ the TOMEs solution.
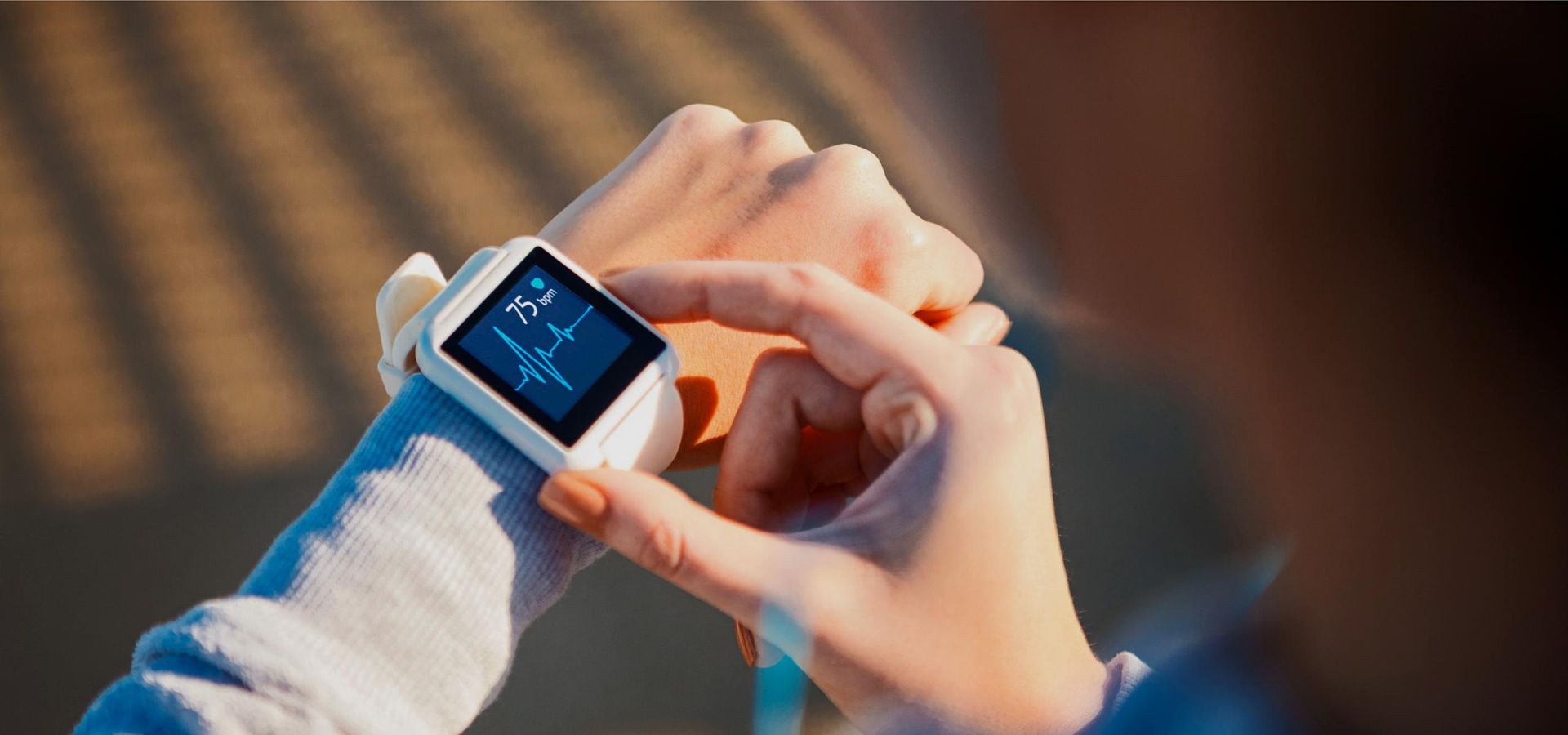
Services
Medical device software development services
As a medical device software development company, Itransition implements apps for precise diagnostics, streamlined care delivery and management. Get a quote.
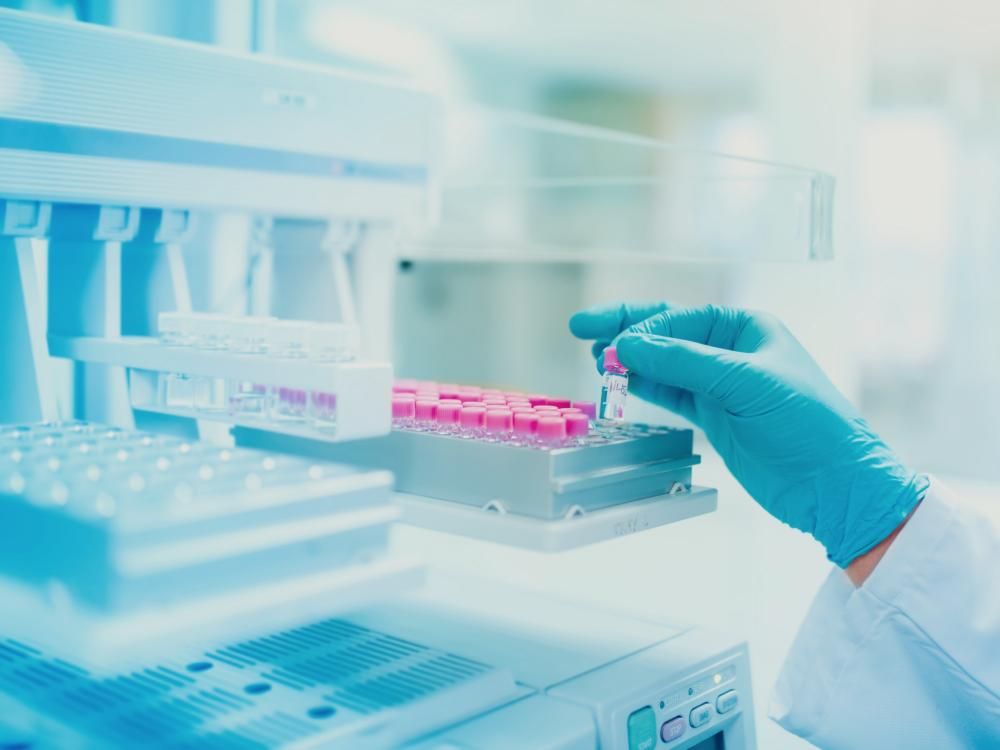
Case study
Pharmaceutical data analytics suite for a US multinational
Read about Itransition’s 10+ years long cooperation with a US-based multinational to create their flagship pharmaceutical data analytics products.
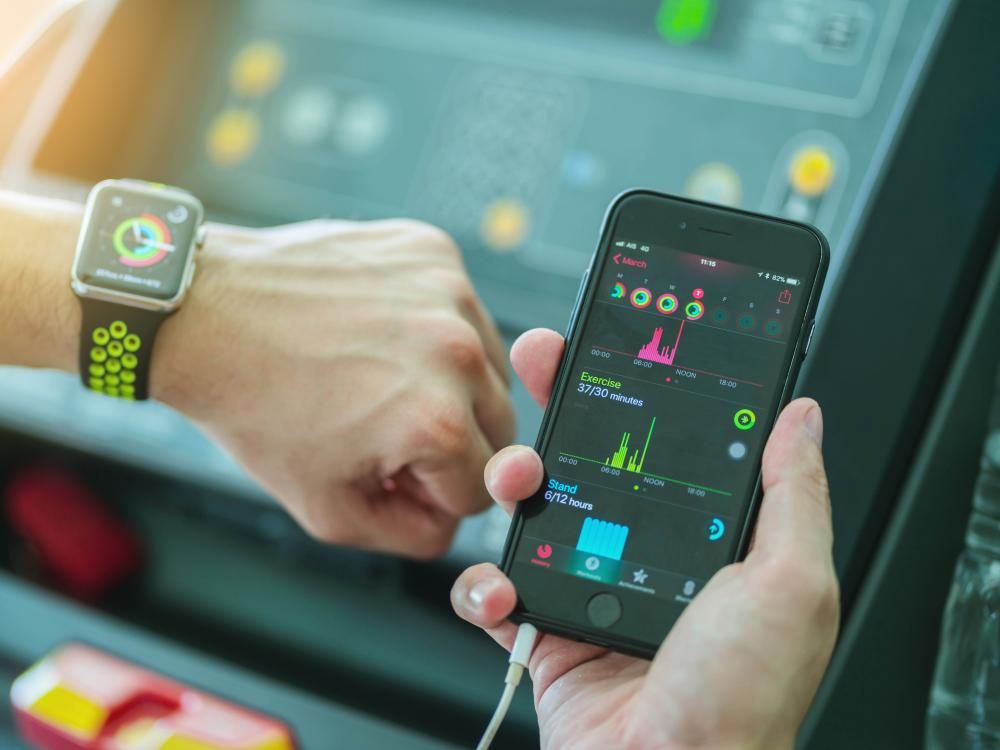
Case study
Cross-platform fitness app suite for adidas
Learn how Itransition revamped adidas’s cross-platform device management backend application and simplified data synchronization process.
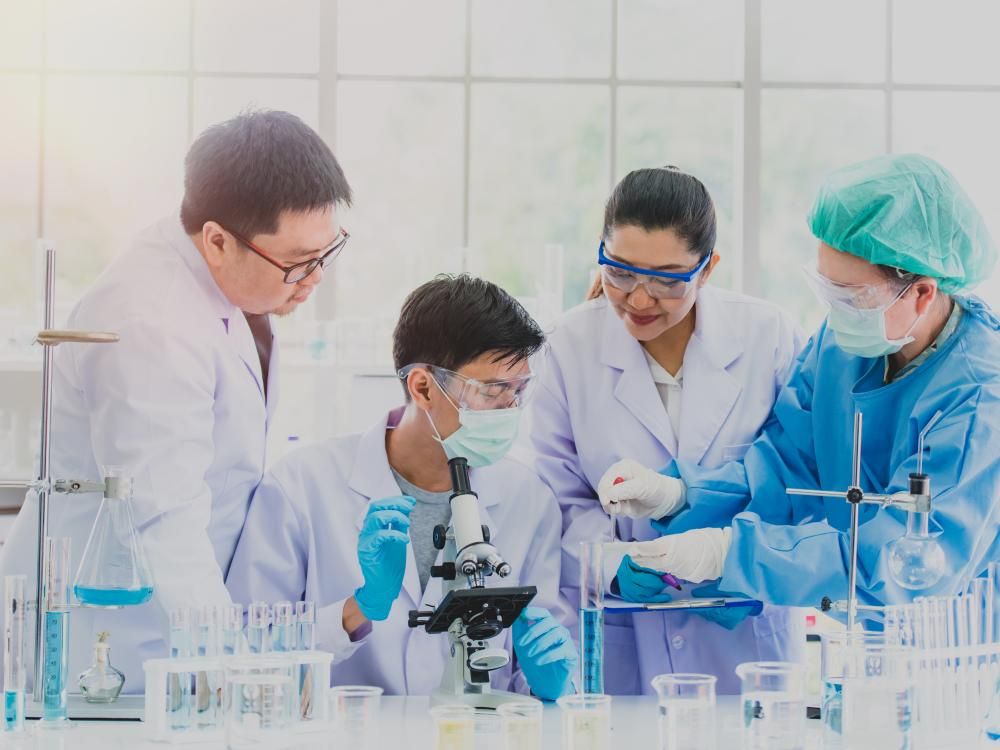
Case study
Healthcare analytics applications revamp for a US multinational
Itransition helped the customer bring their solutions up to speed and further secure their leading position in the healthcare analytics app market.